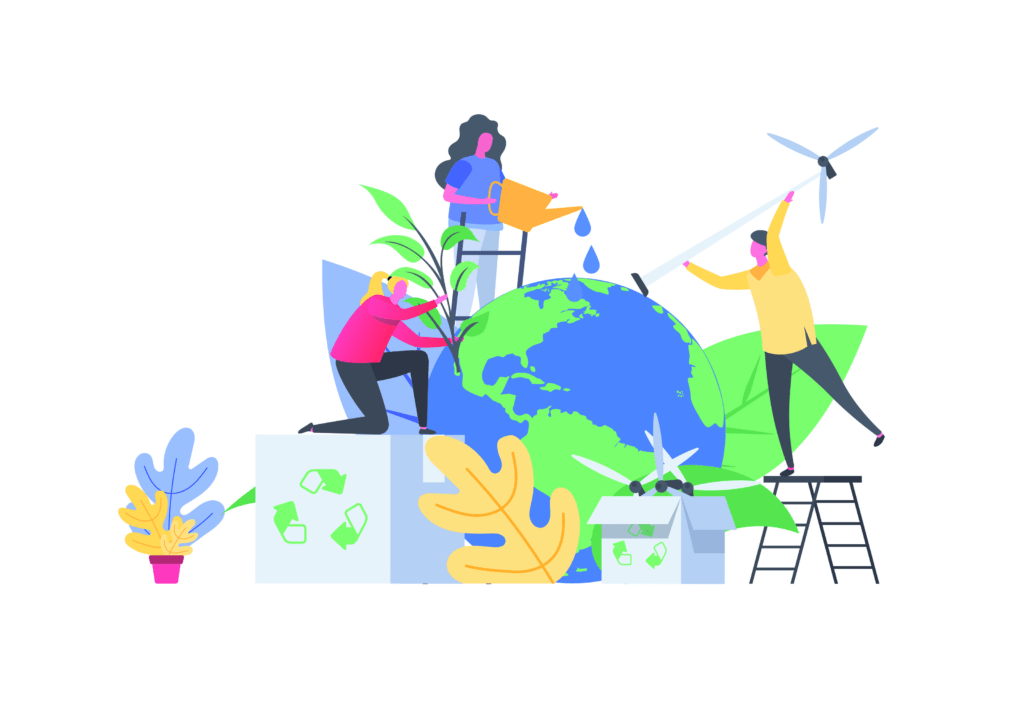
ESG
Message from the Board of Directors
Pro Brand Technology (TW) Inc., (PBT) continues to embrace the concept of sustainable development “Commercial Success, Environmental Protection, Social Responsibility”, and actively promotes sustainable operation and creates long-term value. The Board monitors PBT’s ESG matters in a top-down manner and accepts full responsibility for the strategy and reporting of ESG. PBT has engaged an independent consultant to assist the Board in identifying and assessing material ESG related issues, formulating ESG strategies and measures and addressing existing and potential ESG related risks. The independent consultant will also provide PBT with regular updates on the relevant developments in ESG so as to keep abreast of the latest regulatory and market requirements and assist in preparing for the latest developments. In the post-COVID-19 era, the market is more concerned with how enterprises can mitigate and manage risks and opportunities associated with non-financial activities. PBT has identified and assessed environmental and social risks that have a significant impact on its business and operations and is committed to integrating into its existing risk management policies. In addition, PBT attaches great importance to the stakeholder engagement with a view to enabling all stakeholders to express their views in a full and open manner through extensive and effective communication channels. Same as last year, PBT collected the opinions from stakeholders by a questionnaire and a materiality assessment was conducted by an independent consultant to identify the sustainability issues that are most relevant to PBT’s business and stakeholders, and assist the Board in determining the priorities and strategies for managing the sustainable development.
Sustainability Governance
The establishment of a sustainability governance structure can clearly define the responsibilities of the Board and each functional department in the ESG area and establish effective communication.
SUSTAINABILITY GOVERNANCE STRUCTURE AND APPROACH TO SUSTAINABILITY
The ESG structure is currently divided into two tiers, namely the Board and the ESG team, and its responsibilities are as follows:
Board of Directors
The Board serves as the highest level in the sustainability governance structure, plays a supervisory role to ensure that the business operations are conducted in accordance with the principles of prudent corporate governance for the long-term benefit of shareholders and PBT.
- Formulating sustainability strategy
- Supervising and improving ESG policies, practices and performance, and reviewing and improving various policies and measures on a regular basis
- Responding and managing various sustainability risks and opportunities
- Reviewing the adequacy of resources devoted to ESG matters
ESG team
In terms of execution, the management of PBT is responsible for the formulation and implementation of sustainability strategies at PBT level and reports to the Board on a regular basis. PBT has an ESG team, comprising senior management, representatives from different departments and manufacturing sites of PBT:
- Implementing sustainability measures and tracking the effectiveness of measures
- Gathering ESG data
The Board will regularly review and enhance the effectiveness of the sustainability development governance structure to further improve the sustainability governance of PBT.
RISK MANAGEMENT
The market is concerned about the identification, mitigation and management of sustainability- and climate-related risks and opportunities, including the assessment of the level of exposure and the current and future management measures. PBT has a well-developed risk management and internal control system in place, and has confirmed to the Audit Committee and management about the effectiveness of the measures to be taken during the year while summarizing the corresponding measures during the year, based on the findings of ESG risk assessment in prior years. The key risks identified by PBT are set out below:
Type of ESG risk Description of risk Corresponding measures
- Climate change
- Environmental management
- Waste management
- Health and Safety
- Supply chain management
- Product quality management
Stakeholder Engagement
PBT attaches great importance to the opinions and expectations raised by key stakeholders. After collecting and considering their opinions, the feasible opinions will be incorporated into daily operations to promote PBT’s business development and sustainable development. During the Year, PBT actively established communication channels to regularly contact key stakeholders, including employees, shareholders and investors, customers, partners, contractors, regulators and the community.
Operational Responsibility
Operating responsibilities include supply chain management, product responsibility and anti-corruption. PBT implements the concept of rational management and creates a win-win situation through carrying out standardized regulation through relevant policies and measures in line with the vision of PBT’s long-term brand opportunities.
PRODUCT RESPONSIBILITY
Product quality
Ensuring the quality of products is the priority task of manufacturers, which at the same time can improve satisfaction and protect health and safety. PBT has established stringent control over the quality of its products and services, including a quality management system certified by the GB/T 19001/2016/ISO9001: 2015 at each plant and regulated procedures and standards governing the material acquisition, production, assembly, inspection and storage. PBT also regularly liaises with suppliers to ensure that the raw materials used meet the production requirements.
Each plant has a quality management department, which is responsible for conducting regular quality inspection on raw materials and finished products in the course of production to ensure that all products meet the quality safety standards and requirements. For materials which are stored for too long or which are packed with damaged materials, the relevant authorities will also conduct quality tests again to ensure that they are in good condition before being delivered to the customers.
As PBT is involved in the distributed business, the distribution products are tested for quality control before entering the distribution point to ensure that all the products meet the local standards and requirements for quality safety, and that the non-qualified products are not sold to the customers.
None of PBT’s products were required to be recalled due to safety and health reasons during the year. In terms of product recalls for other reasons, PBT convened quality meetings when necessary to analyze and formulate improvement measures for the products, so as to reduce the recurrence of similar incidents.
After-sales management and customer service
Each year, PBT sends satisfaction questionnaires to its customers to understand their opinions on the products and services. Clients may also lodge complaints and send their opinions to the business personnel through fax or e-mail within a complaint mechanism. If a complaint is received, PBT’s Quality Management department will follow up and investigate in a systematic manner in accordance with the Rule for Handling and Managing Customers’ Complaints, and shall within three working days reply to the customer and discuss with the customer on the solution, including product recall, replacement or repair.
Protecting intellectual property and customer privacy
PBT respects intellectual property rights and protects the privacy of its customers. PBT’s policies such as the Business Ethics Regulations, the Code of Conduct and the Employee Handbook provide procedures for the handling and use of confidential information, including requiring employees to ensure that confidential information of customers and suppliers is kept confidential and strictly prohibiting unauthorized disclosure of such confidential information to third parties. Suppliers are also required to sign confidentiality agreements and commit to complying with the relevant privacy protection policies.
Cyber and information security cannot be overlooked. PBT has installed firewalls, anti-virus and anti-malware programs in the internal information systems and has also established a cyber security incident reporting mechanism in the distribution business to prevent and reduce operational risks arising from cyber-attacks. Our employees are required to collect and process customer data in accordance with our procedures to ensure that the customers’ data do not leak.
Fair and responsible marketing
In terms of product marketing and promotion, PBT ensures that the published contents of the advertising and promotion materials are scientifically evident, without misrepresentation, exaggeration and misleading information, and more importantly comply with the requirements of local laws and regulations through strict guidelines and internal control. PBT’s Business Ethics Regulations provides procedural guidelines for employees that are responsible for marketing and promotion, and requires strict review before launching of the content of advertisements and promotions. The marketing content shall truthfully describe the effectiveness of the product and provide the proper use of it, enabling consumers to make decisions of appropriate choices.
ANTI-CORRUPTION
PBT has always upheld the highest standards of corporate integrity and business ethics.
PBT adopts a zero-tolerance attitude towards bribery, extortion, fraud and money laundering.
PBT has established the Business Ethics Regulations, the Code of Conduct and the Employee Handbook, requiring employees not to accept or solicit gifts and benefits from customers or business partners that undermine the interests and integrity of PBT and not to take actions violating laws and regulations. In addition, PBT also has a Inside Information Policy in place to provide guidance and training to directors and employees in handling and disclosing inside information, so as to ensure that inside information is disclosed to the public promptly in accordance with the Listing Rules. PBT has a whistleblowing system in place to encourage employees to report any misconduct such as commercial bribery through the whistleblowing channel. During the Year, PBT did not receive any corruption-related litigation cases filed and closed against the enterprise or employees.
To enhance the understanding of anti-corruption and corporate integrity culture, PBT provided employees with anti-corruption and employees’ code of conduct training during the Year on how to avoid misconduct such as the transfer of benefits and the use of false documents. PBT also produced posters and translated the contents into Vietnamese language for local employees to better understand the contents. PBT also regularly distributes anti-corruption training materials to the Board, which focus on integrity management, anti-corruption laws in Hong Kong and the integrity and due care of the Directors.
SUPPLY CHAIN MANAGEMENT
PBT engages suppliers in accordance with the policies such as the Procurement Procedures and the Third Party Management Procedures. The strategic suppliers defined by PBT is a third party capable of providing qualified raw materials and processing materials in a long-term and stable manner to ensure that the products purchased or outsourced meet the production requirements. PBT requires potential new third party manufacturers to provide information and arrange evaluation. The evaluation criteria include quality, price, reputation, cooperation case and environmental and social performance.
PBT places emphasis on responsible procurement and the management of environmental and social risk in the supply chain. PBT has formulated the Procurement and Supply Chain Management Policy to provide procurement criteria and guidelines for each business unit. PBT has been working closely with its suppliers on production matters to ensure that the procured raw materials meet PBT’s requirements, such as the requirement to check compliance with toxic chemicals. Meanwhile, PBT also adopted the Climate Change Policy4, incorporating climate change as a factor to be taken into account in procurement and using low-carbon and energy-efficient products and materials as far as practicable. Suppliers are required to sign the Commitment Letter of Suppliers’ Business Ethics and Commitment Letter of Suppliers’ Compliance with Social Responsibility.
As a responsible enterprise, PBT makes reasonable efforts to avoid the procurement of conflict minerals5 obtained by illegal or unethical means. PBT has implemented a conflict minerals compliance plan with suppliers, actively prevent any violence, infringement of human rights and environmental damage involved in mining processes. At the same time, when entering into agreements with suppliers, PBT will also include business ethics clauses and production quality requirements and require suppliers to comply with PBT’s procurement policies.
Caring for Employees
PBT recognizes the dedication and contribution of employees and strives to create a good working atmosphere and to build a healthy and safe working environment in order to enhance their involvement and satisfaction with the work. In addition to offering competitive remuneration and benefits to employees, PBT also provides opportunities for personal development.
EMPLOYMENT AND LABOUR STANDARDS
PBT ensures compliance with employment-related laws and regulations and continually evaluates and improves human resources strategy to ensure that the views of the employees are respected and in line with the market trend. PBT’s Employee Handbook sets out policies and measures in relation to remuneration and dismissal, recruitment and promotion, working hours, holidays, equal opportunities, anti-discrimination and welfare and benefits.
HEALTH AND SAFETY
PBT has established the Employee Health and Safety Policy to create a healthy and safe working environment for staff and regulate the safety of work. In terms of operations of manufacturing plant, PBT takes the “safety first, prevention oriented” approach to production safety and has implemented the “Health and Safety Management Procedures”,
TRAINING AND DEVELOPMENT
PBT has established a Training and Development Policy to formulate an annual training programmer according to the needs of each business unit to enhance their work skills and industry knowledge and maintain their overall competitiveness. Training covers code of staff, staff and production safety, environmental management, quality assurance and customer complaint handling. We provide induction training to new staff to ensure that they are able to adapt to the working environment and perform their duties independently after initial training and practice. In addition, PBT also operates an external training subsidy scheme to encourage employees to receive external training.
Environmental Management
PBT is actively promoting the development of a green office, with a view to minimizing the consumption of environmental resources and minimizing the potential impact on the surrounding environment during its operation. PBT has established the following policies to incorporate good and sustainable practices into its ordinary and usual course of business to operate in an environmentally friendly manner.
PBT’s management is responsible for implementing, monitoring and reviewing the environmental policies and reports regularly to the Board. The duties and code of conduct of the relevant staff are regulated by the Environmental Management System. The Environmental Management Office is responsible for managing and monitoring the environmental performance of all the plants, including “three wastes” emissions and use of resources. For manufacturing business, all the manufacturing plants have put environmental management systems in place and obtained the GB/T 24001-2016/ISO 14001:2015 certification.
EMISSION MANAGEMENT
Air Emissions
The manufacturing plants strictly follow the Exhaust Emission Management Operating Guidelines in treating air pollutants emitted during the production process, use of vehicles and facilities to ensure that exhaust emissions meet the standards in which each plant operates. In respect of production processes, PBT is committed to operating electric welding and tin furnaces in a well-ventilated environment with ventilation facilities switching on, and adopting the “collection, water spray and cyclone dust removal“ treatment process when polishing the surface of aluminum products to control dust emissions. In terms of the use of vehicle, PBT’s company vehicles use low Sulphur or unleaded fuel and idling engines are required to be switched off.
Greenhouse Gas Emissions
PBT continued to engage an independent consultant to calculate and assesses the GHG emissions from its operations for the Year based on national and international standards such as the “Guidelines for Accounting and Reporting Greenhouse Gas Emissions – Electronic Equipment Production Enterprise” issued by the National Development and Reform Commission, and the GHG Protocol.
WASTE MANAGEMENT
We explore measures to reduce waste at source, including reducing the use of plastic, increasing the use of renewable energy and recycling alternatives, or introducing reusable or recyclable products. We are discussing with our suppliers on ways to change packaging to enhance recyclable and reduce packaging waste, and to inform our customers of our efforts to reduce the use of plastic, reuse and recycling in order to generate synergies to drive the industry to change packaging.
E-Waste Management
PBT including its subsidiaries and its associated companies is committed to promote environmental protection, ensuring safety, health and human rights of the workers to fulfill its corporate social responsibilities. PBT aims at implementing the following directives with express intent to fulfill the following:
- Abide by environmental and labor laws, regulations and other requirements to meet global environmental protection, labor rights and zero-hazard activity.
2. Educate the entire staff, marking them aware to protect the environment.
3. Respect the dignity of lift, cherish natural resources, ensure safety and promote physical and mental health of everyone.
4. Enhance the waste handling and monitor it. The responsible unit shall ensure the wastes handling from mot being reused nor re-sold in order to safeguard the company and customer’s rights.
5. Enhance the monitoring and improving of pollutant and risk management to reduce the impacts on the environment and employees.
6. Promote the independence and reliability of the self- management so as to become an entirely green enterprise.
7. Establish a management system for corporate social responsibility to improve the efficiency for environmental protection, ethics, labor rights, safety and health.
8. Implement greenhouse gas inventory and reduction program to meet international trends in environmental protection and customers’
9. Openly pledge the company’s commitment in protecting the environment and labor rights and reducing occupational hazards. The stakeholder is included in the scope of our commitment.
10. Abide by ethics code of conduct, including business integrity, no improper advantage, not to bride or take bribes, and to protect the personnel who raise any concerns or inform against illegal acts from being fear of retaliation.
PBT also demands that all its suppliers strictly adhere to applicable laws and regulations, respect environmental protection, prohibit children or non-voluntary laborers, treat the workers fairly, reject any kind of discrimination and refrain from purchasing the so-called “conflict mines” to avoid supporting military conflicts and human rights abuse. PBT declares and undertakes not to accept the metal from the “conflict mines”, striving to fulfil our responsibilities as global corporate citizens, pursue business growth while advancing ESG, and contribute to the positive development of the environment, society, and economy.
Note: Conflict metal refers to the minerals from the Democratic Republic of the Congo. Metals of concern are refined into Tantalum (Ta), Tin (Sn), Tungsten (W) and Gold (referred as 3TG).
RESOURCE MANAGEMENT
We explore measures to reduce waste at source, including reducing the use of plastic, increasing the use of renewable energy and recycling alternatives, or introducing reusable or recyclable products. We are discussing with our suppliers on ways to change packaging to enhance recyclable and reduce packaging waste, and to inform our customers of our efforts to reduce the use of plastic, reuse and recycling in order to generate synergies to drive the industry to change packaging.
Energy
During the Year, the Group’s energy consumption was 3,054.3 MWh and the energy density was 0.117 MW per square meter. Due to business needs, the manufacturing business increased the use of company-owned vehicles, hence the petrol and diesel consumption increased.
- The distribution business decreased the consumption of natural gas
- Due to reduction in operating areas, the purchased electricity of the distribution business decreased
- The distribution business has one less set of solar panels.
Our U.S. office of distribution business has also installed solar panels to generate electricity on its own and generated 2.76 MWh of electricity for use in the office this Year. Our goal is to reduce emissions from traditional combustion engines used in our vehicles through electrification, the use of alternative fuels, advanced technology and state-of-the-art operations.
Water Consumption
Water shortage is an ever-growing problem and we seek to manage our activities by way of protecting and cherishing our water resources. In addition, The Group sourced water from municipal supply system and faced no issue in sourcing water fit for purpose.
Wastewater Management
Wastewater produced by PBT mainly comes from industrial wastewater from the operations of our plants, and the domestic wastewater generated from the operation of our offices. There was no relevant record on wastewater generation of PBT during the Year. Our plants have obtained the discharge permit issued by the Environmental Protection Bureau, and have formulated the Guidelines for Wastewater Discharge Management to standardize the process of wastewater treatment in the plants that all the sewage to be discharge shall meet the discharge standard before it can be discharged into municipal sewers. In order to reduce the amount of wastewater discharge, each workshop will recycle the sewage to cool off wastewater, and design a clean wastewater treatment plan.
Environment and Natural Resources
PBT pays attention to the impact of its business operations on the surrounding environment and natural resources and is aware of possible serious environmental incidents, such as air pollution, soil and water contamination, as a result of chemical spills, liquefied petroleum gas explosions and fires in the course of its operations. To this end, the manufacturing plants have formulated the Environmental and Safety Emergency Plan and implemented various emergency and preventive measures, including strict control of chemicals and liquefied gas cylinders in the plants and regular inspections, as well as training and emergency drills for employees using the relevant chemicals, so as to ensure that employees are adequately equipped to deal with potential accidents and safety hazards.
In order to fulfil our corporate environmental responsibility, the manufacturing plants and distribution business have implemented the following resource saving and energy efficiency measures to reduce operating costs while minimizing the impact on the environment. The manufacturing plants have established the guidelines for “Three Wastes” emissions management and the Guidelines for Resource-conserving and Energy-saving Operation” to provide guidance to all units and employees to ensure effective implementation of those measures. Green office management requirements and environmental awareness training are provided to employees at the manufacturing plants and distribution business. Environmental messages are also conveyed to employees through internal newsletters to enhance their awareness of environmental protection. For example, in terms of the common use of paper and raw materials by employees, PBT encourages employees not to print or adopt double-side printing to save the production of paper, and use electronic communication and electronic archiving, prioritize environmentally friendly products or materials during procurement process and reuse internal document folder whenever possible.
CLIMATE CHANGE
Climate change has been identified as the risk that will have a significant impact on PBT and PBT’s assets and businesses will be adversely affected under both the physical and transitional risks. PBT has formulated the Climate Change Policy to evaluate the risks and opportunities from climate change through addressing the framework and guidelines on climate change, and mitigate the risks and impacts of climate change on PBT. At the same time, in order to protect the safety of employees and minimize the impact, PBT has formulated the Contingency Plan for Coping Typhoons and Floods to provide corresponding policies and relevant training under extreme weather conditions.